Academia meets industry… and vice versa. Denmark holds a strong position in the delicate art of making theory and practice blend blood, ultimately benefitting both academic societies and private companies as well as the world outside.
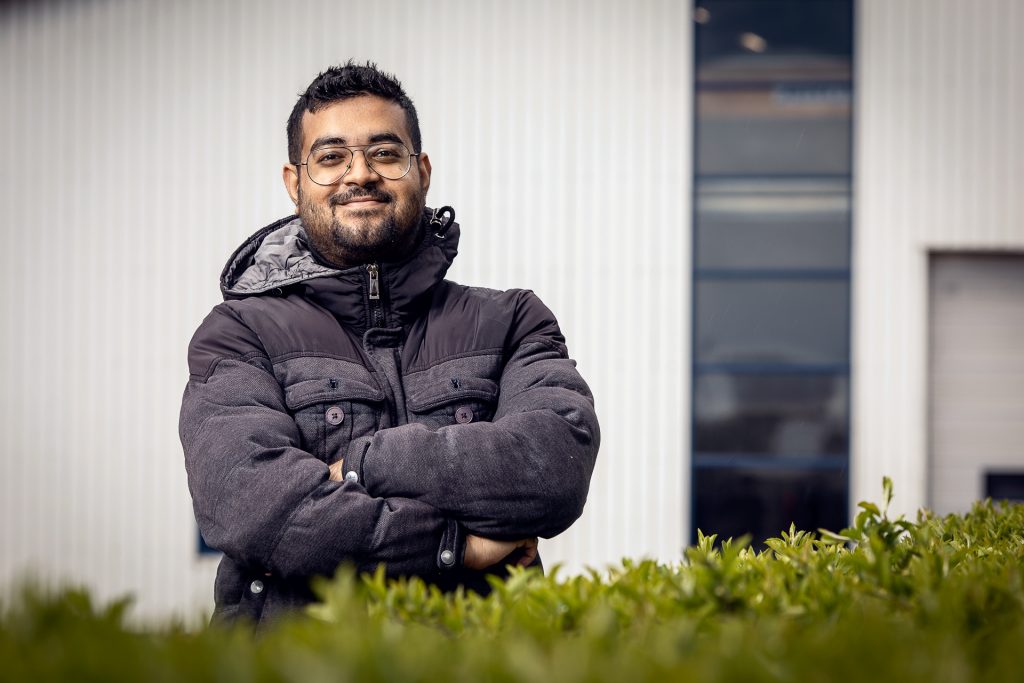
Photo: Anders Trærup, freelance photographer
If – for some reason – you want to know when any given component will eventually fail or break down Khandokar Abu Talha (26) from Bangladesh is a young expert, you should consider paying a visit.
Significant new knowledge
The fellow European Industrial PhD project between the University of Southampton and Vestas aircoil involves four young talents from abroad. The project is funded by the EU Horizon program. The project is planned to last four years with a 50/50 split between studies in the UK and Denmark. The PhD’s have weekly online meetings with their university supervisor and biweekly meetings with their industrial supervisor. At Vestas aircoil the industrial supervisor is Claus H. Ibsen, Master of Science in Engineering (M. Sc. Eng.) and PhD himself.
A PhD (Doctor of Philosophy) is a 3-year postgraduate doctoral degree, awarded to students who complete an original thesis offering a significant new contribution to knowledge in their subject. PhD qualifications are available in all subjects and usually the highest level of academic degree a person can achieve.
Given his capacity to predict the lifespan of a wide range of materials and structures, one could, in fact, argue he is a master of disaster. Yet, engineers don’t use that kind of language which seems a fairly good reason to have Mechanical Engineer and PhD Talha explain himself:
“My work is to investigate the fatigue behaviour of components in a certain structure… let’s say a heat exchanger. Combining fatigue testing with cyclic amplitude loading, observations and merging these real-life data into established and well-proven general theories and methods, I can predict when the component will fail. In a fairly precise manner”.
Using heat exchangers as an example to illustrate his point doesn’t come by accident. Talha is currently working on his PhD thesis, Fatigue evaluations of additive manufactured materials in novel heat exchanger design in the headquarters of Vestas Aircoil – for the past seven decades, a pioneering and market-leading Denmark-based manufacturer of marine and industrial cooling systems.
Knowing what we don’t know
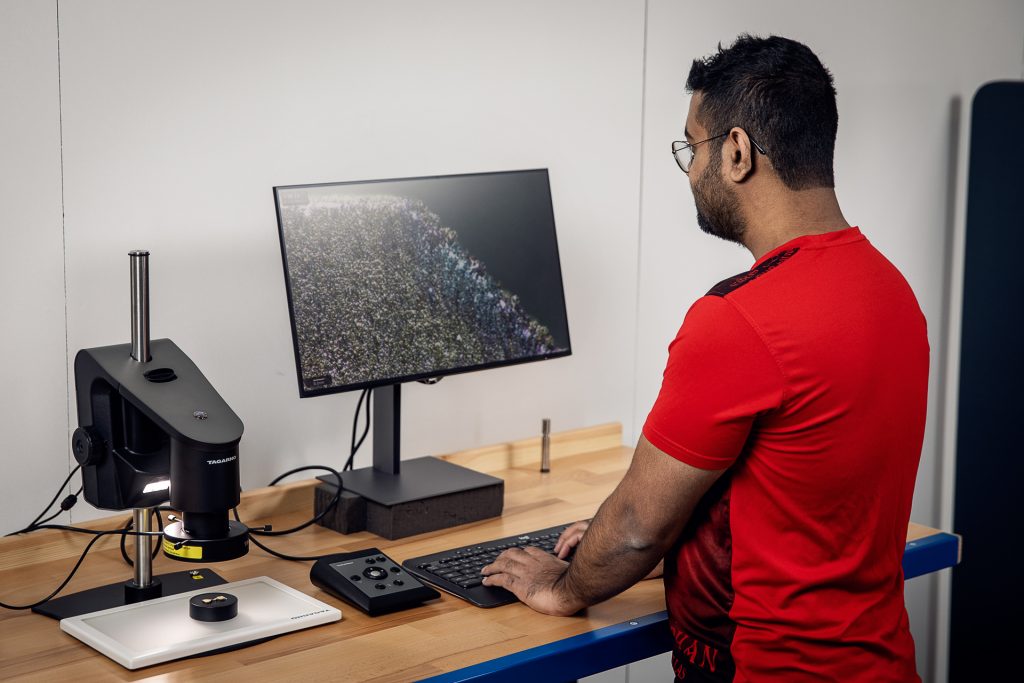
“As goes for any PhD thesis, however, my work has the essential second part not just to obtain an in-depth understanding of what we can observe and already know but indeed carry on the thought process to a next level enabling us to realise some of the knowledge gaps we still face. Realising what we don’t know is a fundamental first step in science to build new experiments that will generate more information and data upon which we can crystallise out groundbreaking new evidence and knowledge”.
Predicting failure in a modern setting basically involves extremely heavy data, capable computer modelling and real-life cyclic loading tests. Inside Talha’s modern computer and its powerful models, however, sits knowledge, part of which goes way back in time.
Understanding the cyclic behaviour of material goes back to World War II. In 1943 two American scientists working for NACA (National Advisory Committee for Aeronautics, the predecessor to NASA) established the Ramberg-Osgood equation that describes the non-linear relationship between cyclic stress and strain, which still is a relevant and widely used theory even though more advanced models are available.
Supporting 65,000 researchers
With the Marie Skłodowska-Curie actions (MSCA) the EU Commission is supporting the career development and training of researchers. The MSCA are expected to finance around 65,000 researchers, including 25,000 doctoral candidates. The EU target is to spend 3% of EU GDP on research and development by 2020. At the MSCA start in 2014 at least 1 million new R&D jobs had to be established.
By funding excellent research and offering attractive working conditions, the MSCA offer high quality professional opportunities open to researchers of any age, nationality or discipline.
The specific objectives of the Marie Skłodowska-Curie Innovative Training Networks (ITN) are:
1. to train a new generation of creative, entrepreneurial and innovative early-stage researchers able to face current and future challenges and to convert knowledge and ideas into products and services for economic and social benefit
2. to raise excellence and structure research and doctoral training, extending the traditional academic research training setting, incorporating the elements of Open Science and equipping researchers with the right combination of research-related and transferable competences
3. to provide enhanced career perspectives in both the academic and non-academic sectors through international, interdisciplinary and intersectoral mobility combined with an innovation-oriented mind-set.
From elastic to plastic behaviour
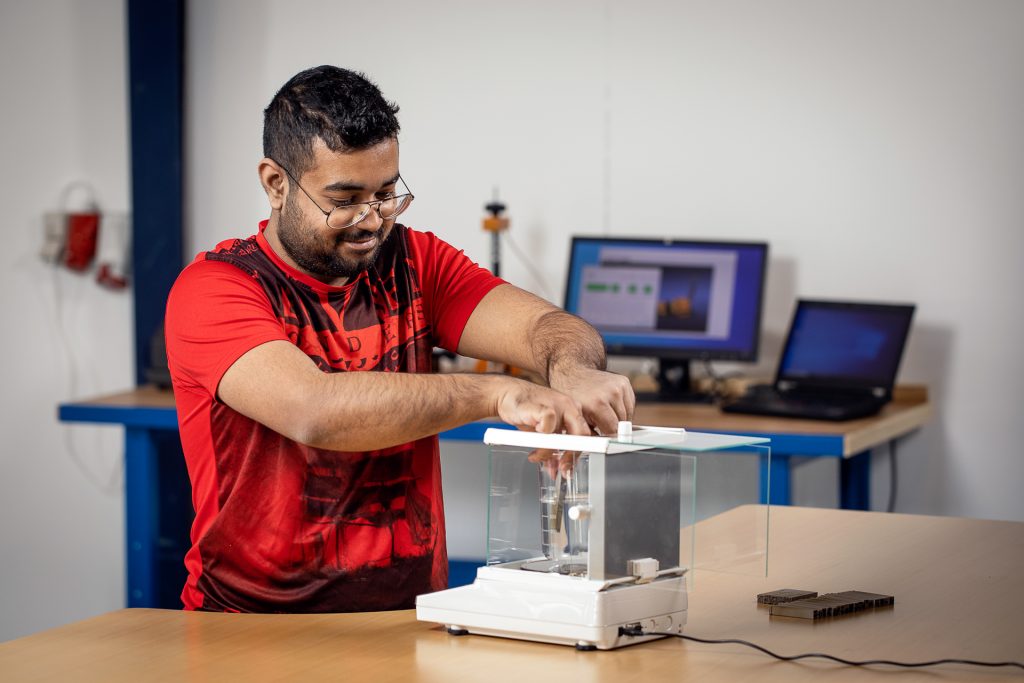
The constitutive equations themself are so complicated it would probably take an engineer to fully understand it.
Yet, the stress-strain curve related to the constitutive equations illustrates the behaviour of materials near the yield points.
In material science and engineering, the yield point is the point on a stress-strain curve that indicates the limit of elastic behaviour and the beginning of plastic behaviour. Below the yield point, a material will deform elastically and return to its original shape when stress is stopped. Once the yield point is passed, however, some fraction of the deformation will be permanent and non-reversible. That stage in the process is known as plastic deformation.
And plastic deformation can often lead to microscopic cracks that, in themselves, are not destructive but can develop further and make the material or structure deteriorate into weakness, malfunction and eventually total breakdown.
A process well-known from numerous incidents and accidents – recent examples being airplane accidents in the US and Europe with engine parts ripping off due to metal fatigue and consequently damaging the entire structure.
Everything will fail one day
“The cyclic behaviour combined with stress-life – the number of cycles to failure under a certain stress level – can predict failure of a structural material with reasonable accuracy. It all started in 1837, when a german engineer, Wilhelm Albert published the first article on metal fatigue, later which was termed as ‘metals being tired’ by Jean-Victor Poncelet, a French engineer. Then, O. H. Basquin proposed the relationship between stress and number of cycles to failure, which marked a major milestone in fatigue research history. For generations, engineers stood on the shoulders of these pioneers, and created complex models of fatigue failure as phenomena and how to excel the prediction of it”.
The pioneering nature of these early realisations proves themselves on a daily basis as theories turn out to be applicable not only to metal as they originated from but – at least partly – also to other materials such as composites, plastics and ceramics.
At the coffee machine in the Vestas aircoil reception area, we briefly dwell at the slightly more philosophical truth that everything may eventually fail. Any structure we build, any machine we manufacture will fail at last. Even human beings and what goes beyond our wildest imaginations have an end:
“Ultimately, even the universe as we know it will possibly collapse one day… in what is to become the biggest failure ever,” Talha says with contagious laughter. “But I am not sure my computer models are capable of predicting much in that context”.
Pioneers for six decades
Founded in the 1950s Vestas aircoil has been a market leading manufacturer of marine and industrial cooling products ever since. Vestas built the first marine diesel engine charge air cooler in the world for Burmeister & Wain in 1956. The company is headquartered in Lem, a small industrial town often associated with its blacksmith industry.
Until the 1980s Vestas aircoil was part of Vestas Wind Systems also located in Lem. Today, Vestas aircoil is owned by Genua. Vestas aircoil has 250 employees based in Denmark, Southern Europe and the Far East.
www.vestas-aircoil.com
Young talents from abroad
In other words: Fatigue, failure and collapse is a law of nature. And Talha’s engineering nature is to describe and predict.
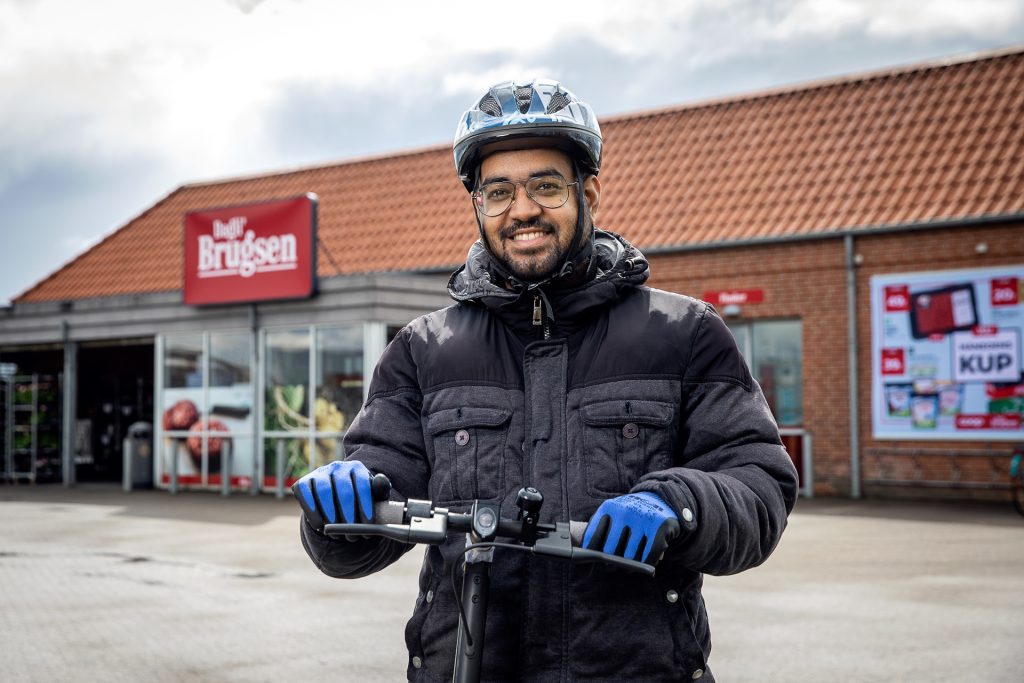
“Predictions of failure are highly relevant in, let’s say, the car industry. Most failures – probably 7 or 8 in 10 – have a cyclic nature. Fatigue cracks in materials and components will correspond in a certain ratio with the numbers of miles the car has been driving. On top of that comes other crucial factors such as climate, load, user characteristics etc. Predictions basically enable companies to set up maintenance schedules, guarantees, spare part production etc. In fact, to a large extent the core business model itself”.
Working closely together with PhD-colleagues Milena Watanabe Bavaresco from Brazil and Kevin Jose and Atul Singh from India, Talha is part of the ambitious research and development team at Vestas aircoil currently planning to further expand its R&D facilities and activities in Denmark.
Three years ago, the market-leading Danish manufacturer of marine and industrial cooling systems joined forces with the University of Southampton in preparations for a fellow European Industrial PhD project financially supported by the EU Horizon program. The international collaboration, including UK, Denmark, the European Union and talented young people from abroad carry the ambition to spark even closer cooperation between academia and industry for their mutual benefit.
“Representing academia, I find the industrial environment very rewarding. It’s indeed inspiring to face real-life challenges. Another upside is the potential networking and collaboration opportunities enabling us to generate new solid knowledge essential for the PhD”.
The deadly winter in Denmark
Talha will work on his thesis at Vestas aircoil until December 2021. Going back to the UK, he will finish his PhD at the University of Southampton within 6-9 months.
Where prediction and failure will bring him after that he doesn’t know yet:
“Before arriving in Denmark, I worked in Bangladesh, France, Germany and England. I am open to any opportunity. Given the current Covid-19 situation… who knows what travel bans will look like in the future?”.
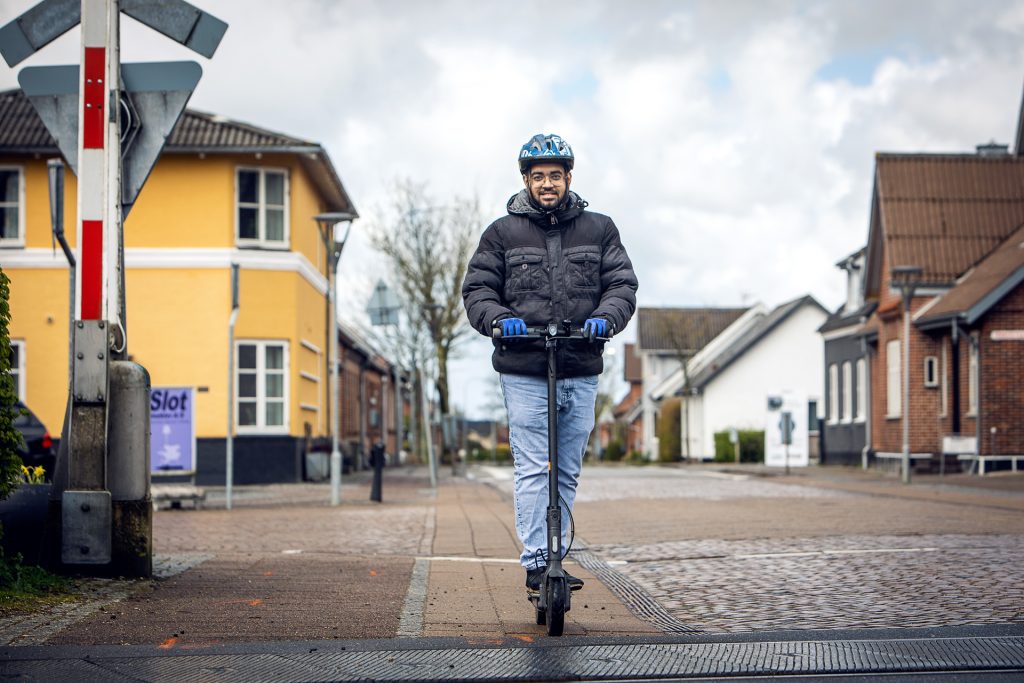
Instead, Talha puts a lot of energy into his passion for cooking. Often together with PhD colleague Kevin Jose from India.
“I am very excited about both the Asian and European kitchen. Coming to the sparsely populated Western part of Denmark, we have realised, however, the difficulties in finding those ingredients we are familiar with in Southeast Asia”.
“Apart from the Asian food resource scarcity, living in Ringkoebing and Denmark has been a wonderful experience so far. People are fun and very nice. I am quite excited about the Nordic work-life ratio allowing me substantial time to enjoy the sea and re-energise. The one thing I don’t like about Denmark is winter. No life… no sunshine. It’s deadly!” says Talha with a smile and wraps up:
“And yet I survived…”
Kevin: “Now I see structures everywhere”
Milena: “I fell in love with research”
Atul: “Finding trade-offs is my trade”